
Swansea University
Prifysgol Abertawe
Our Work
Scrap intensive steel production has ~ 75% lower CO 2 emissions than ore-based production and scrap, or End-of-Life (EoL) steel, is likely to be the primary decarbonisation vector for the 7% of global CO 2 emissions produced by the sector.
Unfortunately, UN SDS and world steel data predicts ~1BnT annual global shortfall in scrap availability vs steel demand by 2050. It will be unequally distributed and concentrated in developed economies meaning developing countries (with highest demand) may struggle to access it if emissions reductions targets are to be met. Sustainable high quality scrap management practices underpinned by UNFC and UNRMS are therefore critical to manage this finite resource and maintain it at high quality.
This work in the centre is concentrated on providing the evidence, knowledge and technology required to transform EoL steel management and in doing so ensure the long- term sustainability of manufacturing sectors reliant on high quality steel products.
This involves moving away from the current recycling paradigm illustrated in Fig.1. Currently, extensive product development has produced advanced alloys with transformative benefits in use but has narrowed the available processing windows to produce them. Poor EoL steel management practices result in high levels of contamination from non-ferrous materials and by mixing different steel alloys. This is then returned to a sensitive steel production process creating detrimental impacts on product functionality.
In the new paradigm (Fig.2) reformulation of contamination tolerant steel alloys will expand the process window. At end of first life, data from the use phase and the steel production process can be used to inform re-use, repair, remanufacture or as a last resort recycling of the material. When ultimately recycled, the product data will be used to segregate both the non-ferrous and ferrous fractions of the feedstock, sending elements back to the alloys that require them with minimum cross-contamination.
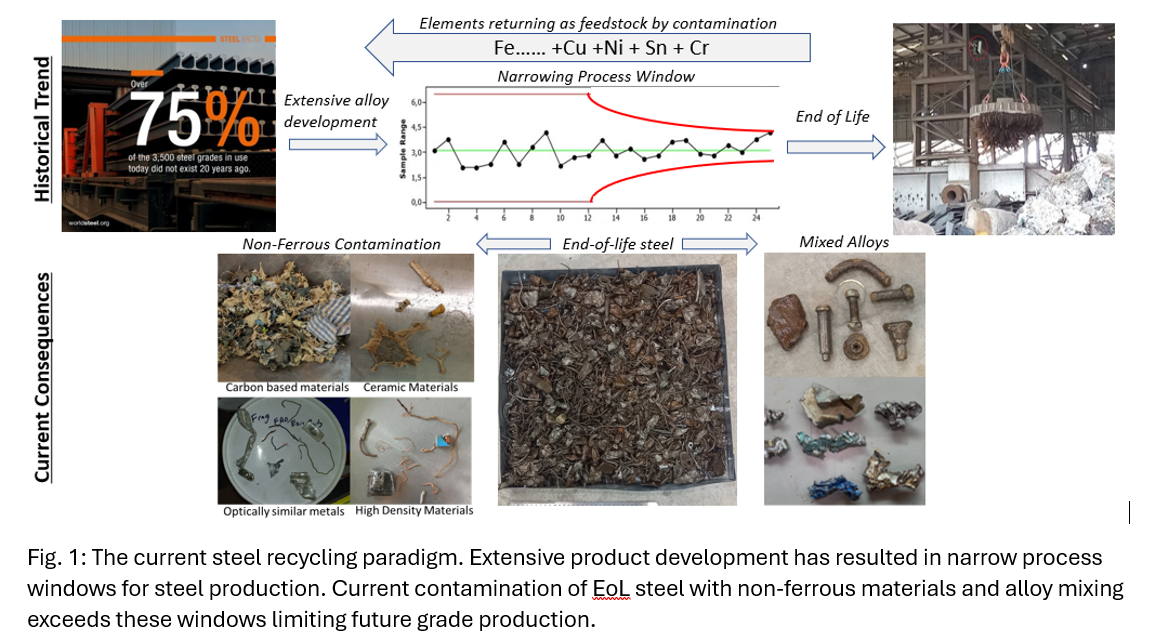
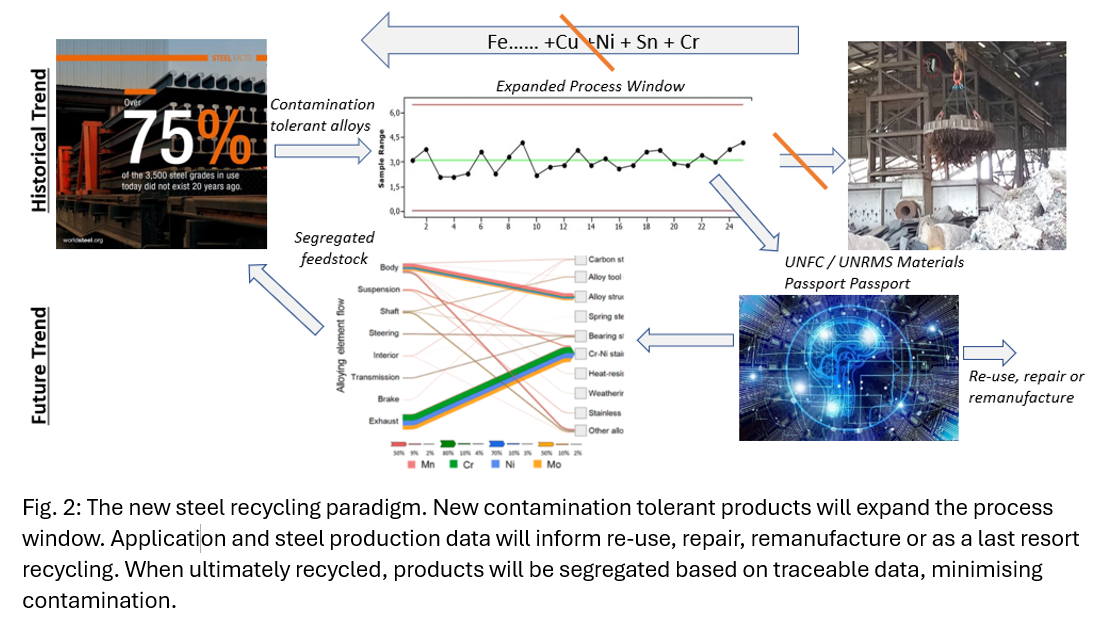
Our Plans
Delivering this requires new standards for EoL steel, new approaches to handling it, innovation in data transfer across the supply chain and robust sampling and measurement practices to validate these interventions. Progress on these aspects will be delivered through a portfolio of projects that implement UNFC and UNRMS assessments to generate case studies.
Broadly this work will:
- Generate EoL steel resource quality & value-in-use data.
- Develop and disseminate measurement & quality standards for EoL Steel.
- Complete attributable and consequential Life Cycle Analyses.
- Produce UNFC & UNRMS case studies that for anthropogenic resources & explore best practice in materials passporting.
This work aims to build a shared technical foundation for managing EoL steel as a critical circular resource, supporting low-emission manufacturing systems globally.
Contact
info.sustainsteel@swansea.ac.uk
Team
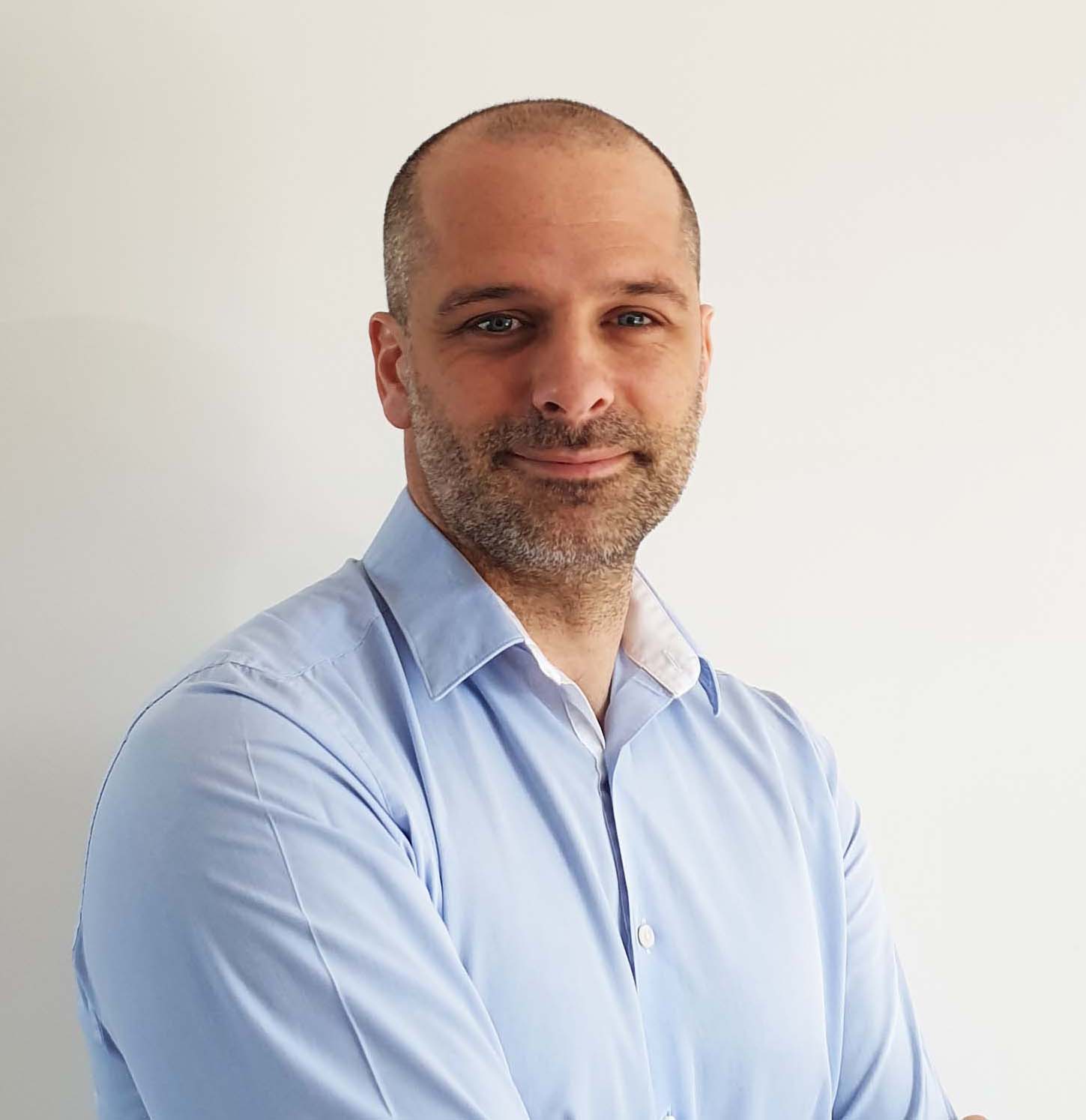
Cameron Pleydell-Pearce
TATA Steel Chair
Cameron holds a Tata Steel chair in steel processing at Swansea University. Alongside his Director role in the UN International Centre of Excellence he is Director of the SUSTAIN EPSRC Future Steel Manufacturing Research Hub (www.sustainsteel.ac.uk). His research centres around the foundation industries, specifically in the metals sector, where his key goal is to support the delivery of cutting edge science and the engineering research required to create carbon neutral, resource-efficient UK steel supply chains.
Cameron has a long history of interfacing with industry and has significant experience of managing industry/academic research collaborations and relationships.
Latest Reports
No Results Found
The page you requested could not be found. Try refining your search, or use the navigation above to locate the post.